Crushing
combines our industry leading crushing solutions and expertise with bulk ore sorting technology to increase the volume of mineable tons, which increases resource …
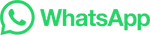
combines our industry leading crushing solutions and expertise with bulk ore sorting technology to increase the volume of mineable tons, which increases resource …
8.1. Introduction. Hematite and magnetite iron ores are the most prominent raw materials for iron and steel production. Most of the high-grade hematite iron ores are typically subjected to simple dry processes of crushing and classification to meet the size specifications required for direct shipping ore (DSO).
The ore crushing process includes four types: ore coarse crushing, ore medium crushing, ore fine crushing, and ore superfine crushing. Ore coarse crushing is …
Copper (Cu) ore is a naturally occurring mineral deposit that contains copper in varying concentrations. It is an important industrial metal that has been used by human civilizations for thousands of years due to its excellent electrical and thermal conductivity, high ductility, and resistance to corrosion. Copper is widely used in various applications, …
The earliest, and simplest method of crushing ore was the use of arrastras. When enough capital was available, stamp mills replaced arrastras at most mines. The following sections take a look at various types of stamp mills, the most common milling facilities at mines of the frontier West. The Trench mill at Silver City, Nevada 1877.
Expert-verified. Outline the general approaches for the isolation of transition and representative metals from natural sources Question Fill in the blanks to complete the sentence below. The isolation of metals from metal ores occurs in three principal steps: First, which may involve both physical changes, like crushing or grinding, and ...
The particle-size crushing effect of different ores is different, which may also lead to the reversal of the crushing effect of pyrrhotite and sphalerite on ores at –16 mm. ... Sun, Y.S.; Yang, J.L.; MA, S.J. Multi-scale impact crushing characteristics of polymetallic sulphide ores. T. Nonferr. Metal. Soc. 2019, 29, 1929–1938. [Google Scholar]
In order to quantitatively analyze the impact crushing characteristics of mineral components in ores, this paper takes pure mineral quartz, pyrrhotite, and pyrite as the research objects and uses …
In mineral processing or metallurgy, the first stage of comminution is crushing. Depending of the type of rock ( geometallurgy) to be crushed, there are 2 largely different techniques at your disposition for crushing rocks. In principle, compression crushing is used on hard and abrasive rocks by placing them between a high wear …
Run of mine ore undergoes an initial process of crushing, milling and classification to generate particles of a sufficient size and mineral liberation. This is …
11.24.1 Process Description1-6. Metallic mineral processing typically involves the mining of ore from either open pit or underground mines; the crushing and grinding of ore; the separation of valuable minerals from matrix rock through various concentration steps; and at some operations, the drying, calcining, or pelletizing of concentrates to ...
Abstract and Figures. The first process that most of the ores or minerals undergo after they leave any mine, is mineral processing or mineral/ ore dressing. It is a process of ore preparation ...
Mixed zones are common among metals whose ores include both oxide (sensu lato) and sulfide minerals (copper, cobalt, nickel, zinc, sometimes lead and antimony). Oxides are generally nearer the surface and sulfides are below, but in between is an interval where supergene fluids have only partially converted sulfides to oxides and …
Media Attributions; Metal deposits are mined in a variety of different ways depending on their depth, shape, size and grade. Relatively large deposits that are quite close to surface and somewhat regular in shape are mined using open-pit mine methods (Figure 8.1.5 in Section 8.1).Creating a giant hole in the ground is generally cheaper than …
Based on the extensive experience of heap leaching operations, crushed ore agglomeration can be successfully considered and utilized as a pretreatment step for the …
Copper is much rarer, but fortunately can be found in high-grade ores (ones containing a high percentage of copper) in particular places. Because copper is a valuable metal, it is also worth extracting it from low-grade ores as well. Ores are commonly oxides, for example: bauxite (Al 2 O 3) haematite (Fe 2 O 3) rutile (TiO 2). . . or sulfides ...
The basic extraction of metals from ores has the following steps. Grinding and Crushing. The bigger chunks of the ore extracted are crushed and ground in ball mills and crushers. It helps to increase the surface area of the chunks for better chemical actions later. In technical terms, it is called pulverisation.
Fig 3 Types of processing ores. The wet processing (Fig 4) is normally practiced for low / medium grade (60 % Fe to 63 % Fe) hematite iron ore. The wet process consists of multi-stage crushing followed by different stages of washing in the form of scrubbing and / or screening, and classification etc., but the advantage is only partial …
Sulphide ores of elements such as Zinc, Lead and Copper are treated using this method. The sulphur in the ore, ... The methods of extraction of metals are (i) Crushing and pulverization (ii) Concentration or dressing of the ore (iii) Calcination or roasting of the ore (iv) Reduction of metal oxides to free metal (v) Purification and refining of ...
Crushing – Involves busting the ore rock into smaller sizes to optimize the subsequent grinding process. ... These contaminates require removal during the varying metal refinement processes. Ores Oxides; …
Metal ores are generally oxides, sulfides, silicates (Table 23.2.1 23.2. 1) or "native" metals (such as native copper) that are not commonly concentrated in the Earth's crust, or "noble" metals (not usually forming compounds) such as gold (Figure 23.2.2 23.2. 2 ). The ores must be processed to extract the metals of interest from the waste rock ...
The extraction of metals and their isolation occurs over a few major steps: Concentration of Ore – Here the ore is separated from earthy impurities. Isolation of metal from concentrated Ore – Here the ore is converted to its oxide form and then reduced. The steps involved are either calcination or roasting and then heating with a reducing ...
Mining has advanced primarily through the use of two strategies: pyrometallurgy and hydrometallurgy. Both have been used successfully to extract valuable metals from ore deposits. These strategies, without a doubt, harm the environment. Furthermore, due to decades of excessive mining, there has been a global decline in …
1. Introduction. Only 0.004% of tin (rare metal) exists in the earth's crust, and the most important source of tin metal is cassiterite. In nature, cassiterite associates with other minerals to form tin polymetallic ores [[1], [2], [3]].In industrial production, different minerals in tin polymetallic ores have varying grindabilities and require fine grinding to …
In mineral processing or metallurgy, the first stage of comminution is crushing. Depending of the type of rock ( geometallurgy) …
The beneficiation of platinum group metals (PGMs) from pristine (unweathered) sulfide ores has conventionally been conducted through froth flotation, which typically achieves platinum recoveries ...
Crushing develops more efficient particle breaking, avoiding fine particles, and optimizing energy consumption. The liberation step is the grinding process and consumes most of the energy in a mineral …
Platinum group metals are conventionally recovered from high-grade concentrates (typically assay of 200 to over 2000 g/t PGM with 0.4–2.8% Cr 2 O 3) by the traditional matte–smelting–refining technique depicted in Fig. 2 (Cole and Joe Ferron, 2002).Ore is first ground by conventional multistage crushing and ball milling, or by semi …
ores of copper sandstones and slates are primarily pro-cessed abroad. The amount of copper in copper sand-stones and slates varies from 1 to 6%, in sulfide cop-per-nickel ores from 1.1 to 4.9%, in copper-pyrite ores from 0.1 to 3%, and in copper-porphyry ores from 0.4 to 1.2%. Up-to-date technological solutions, effective
To participate in the 911Metallurgist Forums, be sure to JOIN & LOGIN; Use Add New Topic to ask a New Question/Discussion about Crushing.; OR Select a Topic that Interests you.; Use Add Reply = to Reply/Participate in a Topic/Discussion (most frequent). Using Add Reply allows you to Attach Images or PDF files and provide a more complete input.; Use …
حقوق النشر © 2024.Artom كل الحقوق محفوظة.خريطة الموقع