Temperature Measurements in Cement …
The Burning Zone. Also known as the firing zone, the burning zone is at the lower end of the rotary kiln, where the cement components are heated to about 1,300° C to 1,450° C, forming clinker. …
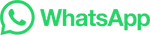
The Burning Zone. Also known as the firing zone, the burning zone is at the lower end of the rotary kiln, where the cement components are heated to about 1,300° C to 1,450° C, forming clinker. …
In the early 90s, grinding in cement plants was operated mainly by vertical mills for raw material with rather good results in the majority of cases, and by tube mills for cement, with some ...
The energy consumption of the total grinding plant can be reduced by 20–30 % for cement clinker and 30–40 % for other raw materials. The overall grinding circuit efficiency and stability are improved. The maintenance cost of the ball mill is reduced as the lifetime of grinding media and partition grates is extended. 2.5.
Find engineering and technical reference materials relevant to Milling Operating System at GlobalSpec. Home. Products & Services. ... Concrete and …
Ball milling media consists of wet, batch units in which water or other liquids and additives aid the grinding process by reducing friction and providing cooling. Ball grinding media uses an abrasive bonded to a wheel, belt, or disc to remove material and improve surface finish. Media mills are also used to disperse powder into a liquid product ...
Finish grinding system. Press equipped with separator and desagglomerator. Cement is ground in roller press only. Rule of Thumb. 1 [kW] absorbed in the press replaces 2 – 2,5 [kW] in the tube mill. If roller press is used as a retrofit for existing systems, capacity increase of. 25 – 50 [%] can be achieved.
Features. Milling machines may include controls that support or include software packages for computer-aided design (CAD) or computer-aided manufacturing (CAM). Programmable machines can be set up for automated or semi-automated operations. Rotary tables allow rotation of the workpiece and provide travel along multiple axes.
A milling device sometimes used for grinding cement and industrial minerals is a grinding table. Figure 8 shows a typical example. It consists of a 4 m diameter table rotating around its centre at 20 rpm. On the …
The tip clearance should be. a) Able to take care of the thermal expansions during the operations. The gear ratio shows it to be a large gear. Our gears with ratio 222/27 ahs a diameter of more than 5m. b) Take care of the profile machiining - the root radius etc should not be damaged during hobbing the involute.
3) grinding aid. Cost 0.6-1.2 €/t, usage 150-400 g/t. As the cement particle gets smaller the pores disappear and no longer become a factor. Increasing the amount of grinding aid will make the cement easier to grind. Hard …
Best practice sharing by Dalmia and Pingyi CUCC for Low Specific Power Consumption, and by LuNan CUCC for Raw Mill Retrofit; Expert sharing by TCRDI, Shangshan South Cement, Deqing South Cement and Hefei Cement Design Institute for Green and Smart Grinding; Round table discussion and Q&A; Register here (WCA …
Tilt tables can be actuated by either hand or foot controls. Some tilt tables will also have a rotating motion. Vibrating features on tilt tables are common to aid in the dumping of viscous or hard to remove contents. Tilt tables can also have lifting action using a number of mechanisms. These include scissor lifts, screw lifts, rack and pinion ...
A Micron-Master Jet Pulverizer jet mill (0.61 m in diameter)was used in this study to grind the materials as shown in Fig. 1 a and b. The materials to be ground were blended for 60 min in a 0.19 m 2 V-blender (this step is only conducted for blends). After blending, approximately 45 kg of the pre-blended material was transferred into the …
Find Grinding Mills and Pulverizers on GlobalSpec by specifications. Grinding Mills and Pulverizers are machines that grind materials into fine powders, tiny shards, shapes, or …
To select a pole shape, consider the application (grinding, milling, drilling, EDM, etc.,) and the size, or range of sizes of the parts that will be held. Other variables, like the distance between the poles, the size of the part …
Ken Thayer | June 02, 2017. Crushers, grinding mills and pulverizers are types of grinding equipment used to transform or reduce a coarse material such as stone, coal, …
A complete modular mobile cement grinding plant includes raw material supply, material dosing, cement mill, cement silo, cement packing, etc. elements. Module 1: Dosing and conveying system. Module 2: Mill, separator, and filter. Module 3: Storage and bulking. Module 4: Packing. Module 5: Tonnage packing. Module 6: Fly ash storage
These types include: Cone or gyratory crushers insert feed via a cone-shape bowl and crush it with a spinning or gyrating head. HPGR (high pressure grinding rollers), roll/roller crushers, or mineral sizers use two large rollers or a roller and a flat surface. The rolls can be serrated, toothed, or smooth. Vertical impactors use the weight and ...
The first tumbling mill to gain reasonable acceptance was designed by the Sachsenberg brothers and Bruckner and built by Gruson's Workshop in 1885, which was subsequently acquired by the Krupp ...
Disc Mill -- DM 200 from Retsch, Inc. The RETSCH Disc Mill DM 200 is used for batchwise or continuous preliminary and fine comminution of medium-hard to hard-brittle solids (up …
The OK mill is more energy-efficient than other cement grinding VRMs, it consistently operates with lower airflow and the lowest power consumption. Featuring a patented cement grinding profile and an integral separator with industry-leading efficiency, the mill consistently uses five to ten percent less power than other cement VRMs.
Ambient air (2.40 kg/kg cement) and clinker (0.84 kg/kg cement) are the main input sources, accounting for 70.33% and 24.66% of the total input (Table 5), respectively. The moisture contained in ...
Cement grinding operation may be performed in one of the following mill setups. Ball and tube mills. Vertical Roller Mills (VRM). Roller press with Ball mill. Ball Mill. Ball mills with high efficiency separators have been used for cement grinding in cement plants all these years. Ball mill is a cylinder rotating at about 70-80% of critical ...
Find the most up-to-date version of SSPC SP 6 at GlobalSpec. UNLIMITED FREE ACCESS TO THE WORLD'S BEST IDEAS. ... dirt, mill scale, rust, coating, oxides, corrosion products, and other foreign matter, leaving staining or shadows on no more than 33 percent of each unit area of surface. ... Surface Preparation Commentary for Steel …
Description: As a result of its narrow sound cone, UT-20-S allows the detection of objects even through the smallest of openings and drilled holes with a diameter of less than 5 mm. Typical Ultrasonic sensors Ultrasonic sensors may be a useful alternative where optical sensors. Operating Distance: 1.18 to 15.75 inch.
Cement milling is the process of grinding together cement clinker, gypsum and other additives to produce a fine grey powder. The resulting material, called "cement meal", is then heated in a rotary kiln to around 2,000°F to produce the finished product known as Portland cement, which can be used for many different construction purposes.
The MPS vertical roller mill - built to last, reliable and energy-efficient - is the optimum solution when it comes to performing several process steps in one unit. Three stationary grinding rollers roll on a rotating grinding table. The material is drawn in between the rollers and grinding table and ground by pressure and shear.
10 Difficult Problems about Raw Grinding with Vertical Roller Mill Systems and their solutions . First : High vibrations. Potential causes: Too many fines in mill feed Material bed on grinding table not stable. Proposed solutions: Increase feed size Adjust crushers Maybe eliminate a crusher. Expected results: Less vibrations Less fine fractions ...
Cement milling is an essential process in the production of cement, and plays a critical role in ensuring that the final product is strong, durable, and consistent. By grinding raw materials into a fine powder, cement milling makes it easier to mix and transport the raw materials needed to create cement, while also providing cost-effective ...
Cement mill separator, or cement separator, is a type of equipment that was widely used in the cement grinding system and raw mill system of cement plants.The function of the separator is to separate the fine-sized particles from the coarse-sized particles, so as to avoid material condensation and over grinding in the mill, and improve the milling …
حقوق النشر © 2024.Artom كل الحقوق محفوظة.خريطة الموقع