The 6 Main Process Fans in Cement factory
Fans in cement industry are heavy duty and perform two basic functions i.e., supply of air or removal of exhaust gases and material handling. There are many process fans that find applications in cement industry such as raw mill fans, induced draft fans, cooling fans, raw mill exhaust fans, coal mill fans and cooler exhaust fans.
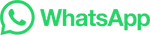