Tanzania: iron sheets production | Statista
Tanzania produced nearly 108,000 metric tons of iron sheets in 2020. The production volume increased from approximately 101,000 metric tons in the previous year. ... Iron ore prices 2000-2022 ...
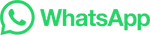
Tanzania produced nearly 108,000 metric tons of iron sheets in 2020. The production volume increased from approximately 101,000 metric tons in the previous year. ... Iron ore prices 2000-2022 ...
Midrex process is simple to operate and involves three major unit operations namely (i) iron ore reduction, (ii) gas preheating, and (iii) natural gas reforming. The heart of the Midrex process is its shaft furnace. It is a cylindrical, refractory-lined vessel and is a key component of the direct reduction process.
Abstract. Mining of iron ore is a highly capital- and energy-intensive process. Life cycle assessment (LCA) of the mining and mineral processing of iron ore in Australia was carried out in this chapter using SimaPro LCA software as a case study. The environmental impacts considered in the study were embodied energy and greenhouse …
a cost-effective flow sheet to beneficiate the low-grade iron ore fines to produce concentrates suitable for blast furnace, pellet and sinter making. Some of the developed …
Iron is an important mineral that helps maintain healthy blood. A lack of iron is called iron-deficiency anemia, which affects about 4-5 million Americans yearly. [1] It is the most common nutritional deficiency worldwide, causing extreme fatigue and lightheadedness. It affects all ages, with children, women who are pregnant or menstruating ...
Find the latest price, historical data, charts and stats of iron ore 62% Fe, CFR China (TSI) Swa on FT.
The iron ore processing flowsheet is consists of two processes:Dry Processing and Wet Processing. The primary beneficiation plant consists of only a jaw crusher and from there the material is transferred to the …
Typical Zinc/Lead Beneficiation Flow Sheet. Multotec specialises in zinc and lead beneficiation equipment with over 50 years of global experience and leading technology. Our team of metallurgists and engineers will partner with you to customise your equipment, helping your process run more efficiently while lowering your overall cost per ton ...
In iron ore-based steelmaking, steel is produced from iron ore. The first step is ironmaking and the main route for iron production is the BF process; 95% of the world's iron production in 2012 ...
The process gases carbon monoxide ( CO C O) and hydrogen ( H2 H 2) are blown into the furnace at temperatures of approx. 1000 °C and flow through the iron ores. The reduction of iron oxides takes place according to the following chemical equations: Fe2O3 Fe2O3 + 3CO + 3H2 → 2Fe → 2Fe + 3CO2 + 3H2O (1) (2) (1) F e 2 O 3 + 3 C O …
resources – natural gas or coal. This process is known as Direct Reduced Ironmaking (DRI). Carbon combines with the oxygen in the iron ore, producing metallic iron and a carbon-rich process gas, according to the following simplified chemical reaction: 2Fe 2 O 3 + 3C -> 4Fe + 3CO 2 It is also possible to reduce iron ore using hydrogen instead
Iron ore is the primary raw material used in the production of steel and — combined with steel — constitutes the world's ... fines 60-63.5% to help clarify the normalization …
Iron ore is the source of primary iron for the world's iron and steel industries. It is therefore essential for the production of steel, which in turn is essential to maintain a strong industrial base. Almost all (98%) iron ore is used in steelmaking. Iron ore is mined in about 50 countries. The seven largest of these producing countries ...
The iron ore pelletizing process consists of three main steps: Pelletizing feed preparation and mixing: the raw material (iron ore concentrate, additives —anthracite, …
Fig. 3 shows a flow sheet of the SL/RN process. Sized lump iron ore (or pellets) and a relatively coarse fraction of noncoking coal are fed into the kiln from the feed end. Coal not only acts as a ...
process flowsheet for the production of sinter- and pellet-grade fines. Experimental Chemistry and mineralogical studies. The iron ore fines sample was obtained from the Bellary-Hospet area, Karnataka, India for beneficiation studies. An iron ore sample of below 10 mm was used for this study. The sample consists of 56.0% Fe, 9.1% SiO 2 and 5.2% ...
The iron ore pelletizing process consists of three main steps: Pelletizing feed preparation and mixing: the raw material (iron ore concentrate, additives —anthracite, dolomite—and binders are prepared in terms of particle size and chemical specifications, dosed, and mixed together to feed the pelletizing process;
Characteristics of iron ore for coal-based process. … +11. Flow sheet of the SL/RN process. ...
The quality of Indian iron ore resources is generally good with high iron content and high percentage of lumpy ore. More than 85% of the hematite ore reserves are of medium- to high-grade (+62% Fe) and are directly used in blast furnace and in direct-reduced iron (DRI) plants in the form of sized lump ore, agglomerated sinter, and …
The iron ore industries of India are expected to bring new technologies to cater to the need of the tremendous increase in demand for quality ores for steel making. With the high-grade ores depleting very fast, the focus is on the beneficiation of low-grade resources. However, most of these ores do not respond well to the conventional …
Price - Chart - Historical Data - News. Prices for iron ore cargoes with a 62% iron ore content rebounded to $105 per tonne after touching a 16-month low of $100 on April 4th, as markets increased their bets of higher demand from Chinese steel producers. Industry groups noted that the large volumes of stimulus from Beijing supported margins for ...
TYPICAL IRON ORE BENEFICIATION FLOW SHEET Fine Product Effluent Pump Dewatering Screen Static Screen Panels Floats Drain & Rinse Screen Gyratory Crusher ROM Stockpile Sizing Screen Sizing Screen ... Process Control Hammer Sampler Fine DMS Cyclone Sieve Bend Housing Boom Stacker Sampler Filter Press MIMS Pump …
The iron ore processing industry produces usable concentrations of iron-bearing material by removing nonferrous rock (gangue) from low-grade ore. In the United States, predominant iron ore is taconite which is a hard, banded, low-grade ore. Ninety-nine percent of the crude iron ore produced in the United States is taconite.
For iron ores with significant amounts of rare-earths [47,[320][321][322][323] [324] [325], the incorporation of rare-earth recovery steps can improve the economy of the ore beneficiation process ...
Iron Ore Price: Get all information on the Price of Iron Ore including News, Charts and Realtime Quotes.
The reduced DRI in the form of hot briquetted iron can also partially replace iron ore in cast iron production in a blast furnace. This allows the coke consumption and, correspondingly, the CO 2 ...
The journey of stainless steel begins with the extraction and processing of raw materials. The primary component of stainless steel is iron, which is usually sourced from iron ore deposits. Iron ore is a naturally occurring mineral that is found in abundance in various parts of the world. The process of extracting iron ore involves mining ...
In BFI, the iron ore is reduced to iron through a chemical reaction with carbon monoxide generated from coke. Coke reacts with oxygen in the iron ore to produce carbon monoxide, which acts as the reducing agent to convert iron oxide into iron: Fe 2 O 3 + 3·CO → 2·Fe + 3·CO 2. BFI is a carbon-intensive process.
The most widely distributed iron-bearing minerals are oxides, and iron ores consist mainly of hematite (Fe2O3), which is red; magnetite (Fe3O4), which is black; limonite or bog …
IRON ORE BENEFICIATION. Your Specialist in Process Equipment. PLEASE NOTE: All Multotec equipment is shown in green. Variations of this block flow sheet will exist based …
حقوق النشر © 2024.Artom كل الحقوق محفوظة.خريطة الموقع