LOESCHE-MILLS
The modular structure of larger roller grinding mills enables uti-lisation of the same components in different mill sizes. Module components include grinding rollers, rocker arms, pedestals and spring assemblies. The principle behind this structure was patented in 1970 and is employed for coal grinding mills and mills in the cement and
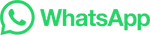